Integrated production system = all -in-one
Organizational structure that enables speedy response
Since our founding, we have carried out all processes in-house, from design to production and delivery. As more and more companies shift their production bases overseas due to the recent turbulent economic conditions, we continue to focus on "added value" manufacturing and integrated production. And the most important thing is the "customer-first mind" that creates quality, value, price, and speed that can be recognized as a partner by sincerely dealing with "customer's troubles". It is this integrated production = all-in-one system that makes this possible, and I believe that each department has a high level of awareness and technical capabilities.
01Sales
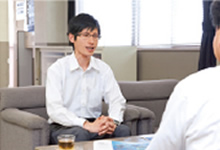
An important contact point for accurately and quickly communicating customer requirements within the company. With "plus one added value" as our motto, we are always trying to make proposals that please our customers.
02Design
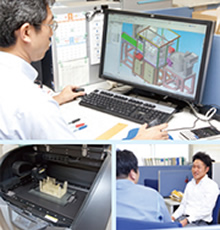
Product development is designed by making full use of 3D-CAD, and the design model is to model the introduced 3D printer, and any concerns are immediately confirmed and verified. Therefore, it is possible to prevent troubles that may occur during mass production as much as possible, which contributes to improving customer satisfaction.
Since all processing processes are located on the premises of the head office, we can quickly communicate between the design and the processing site, enabling "shortening the development period" and "more reliable manufacturing". It is a key department responsible for producing low-cost, high-performance "only one in the world" products.
03Orders & Plans
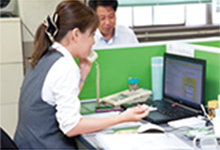
After proposing a prototype to our customers, we will accept orders after they are satisfied with the technical and cost aspects. We will create a production schedule until delivery according to the customer's schedule.
04Mold development
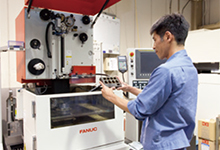
We make molds (framework) for metal parts produced in the processing process. Press progressive dies for automatic tapping inside the dies. In addition, it is possible to design molds compatible with M2.5 to M6.
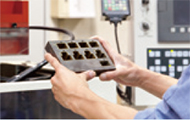
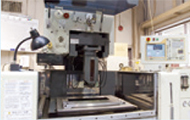
05Processing
Pressing (manufacturing of metal parts) and molding (manufacturing of plastic parts) are performed using the completed mold. The completed parts are inspected by skilled craftsmen before proceeding to the next process.
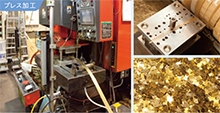
Press working
We have a total of 13 link press machines from 30t to 80t, and can press with a plate thickness of t0.2 to t2.0.
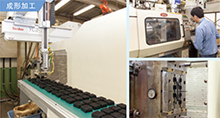
Molding
It is possible to mold thermoplastic resin with a total of 8 units with a mold clamping pressure of 40t to 110t.
Acceptance inspection of processed parts and purchased parts
06Assembly processing line
Assembly of metal and plastic parts by opportunity and skilled workers. We also perform quality checks by workers during assembly. That is also an important task of "multi-skilled workers".
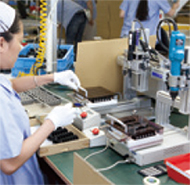
Adopts a cell production method that enables high-mix low-volume production. One worker (multi-skilled worker) assembles three terminal block devices.
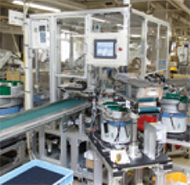
Mass-produced products are automated by machines. Assemble varieties with different pitches of 3P to 7P of the terminal block automatically, accurately and quickly.
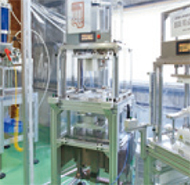
Production work is carried out in a series of steps from cutting stamped parts of insert molded products → withstanding voltage inspection → continuity inspection → visual inspection.
07Shipment
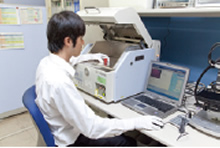
The finished product is inspected thoroughly before shipping. In addition, we are conducting environmental checks on new materials and conducting environmental monitoring for each type of plating bath using a fluorescent X-ray analyzer.
Main production equipment
- Injection molding machine
- 8units
- Torque pack press machine
- 4units
- Link press machine
- 7units
- High speed automatic press machine
- Two
- Machining center
- Two
- Wire electric discharge machine
- Two
- NC milling machine
- One
- NC electric discharge machine
- One
- Molding surface grinding machine
- 3units
- Lathe
- One
- 3D molded parts prototype
- One
- Other electrical measuring instruments
- Set