一貫生産システム=オールインワン
スピーディーな対応を可能にする組織構造
当社は創業以来、設計から生産、納品まで、すべての工程を社内で行っております。昨今の激動ともいえる経済状況で海外へ生産拠点をシフトする企業も増えるなか、当社は"付加価値"のあるものづくり、そして一貫生産にこだわり続けています。 そしてもっとも大切にしているのは「お客様の困りごと」へ誠心誠意向き合い、パートナーとして認めていただける質・価値・価格・スピードを創出する"カスタマーファーストの心"。それを叶えるのはこの一貫生産=オールインワンのシステムであり、各部署における高い意識・技術力だと思っています。
01営業
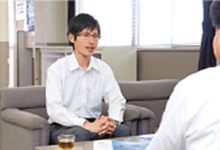
お客様の要求事項を社内に正確かつ素早く伝達する重要な窓口。"プラスワンの付加価値"をモットーに、お客様に喜ばれる提案を常に心掛けています。
02設計
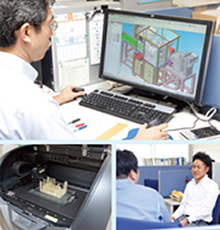
商品開発は3D-CADを駆使した設計を行っており、設計モデルは導入した3Dプリンターを造形し、不安点はすぐに確認・検証します。そのため、量産時に発生しうるトラブルを最大限未然に防止することができ、顧客満足度向上に貢献しています。
当社はすべての加工工程が本社敷地内にあることにより、設計⇔加工現場との意思疎通が素早く図れ、「開発期間の短縮」「より確かなものづくり」が可能に。低コストで高性能な"世界に一つだけ"の製品を生み出す役目を担う要の部署です。
03受注&計画
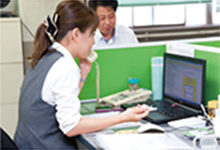
お客様へのプロトタイプのご提案後、技術面、コスト面も納得していただいてから受注へ。お客様の予定に合わせて、納品までの生産スケジュールを作成します。
04金型開発
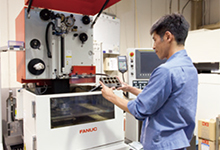
加工工程で作り出される金属部品用の金型(枠組み)を作ります。プレス順送金型で、金型内での自動タップ加工を行います。また、M2.5~M6対応の金型設計が可能です。
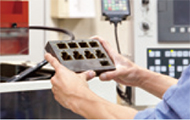

05加工
出来上がった金型を用いて、プレス加工(金属部品製造)と成形加工(プラスチック部品製造)を行います。完成した部品は熟練の職人による検査後、次の工程へ。
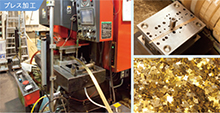
プレス加工
30t~80tまでのプレス機 各種11台を保有し、板厚t0.2~t2.0のプレス加工が可能。
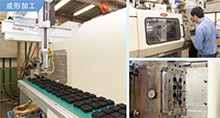
成型加工
型締圧力40t~110tまでのトータル8台での熱可塑性樹脂の成形が可能。
加工部品および購入部品の受入検査
06組立加工ライン
機械と熟練の作業者による、金属部品とプラスチック部品の組み立て。組み立て時にも作業者による品質チェックを行っております。それも"多能工"の大切な作業です。
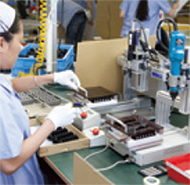
多品種少量生産を可能にするセル生産方式を採用。一人の作業者(多能工)が端子台の装置3台の組み立て作業を行う。
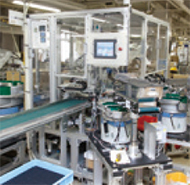
多量生産のものは機械で自動化。端子台の3P~7Pのピッチが異なる品種を自動で的確かつ迅速に組み立てる。
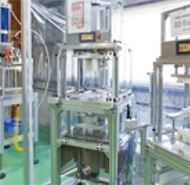
インサート成形製品のプレス部品カット→耐電圧検査→導通検査→外観検査まで一連の流れで生産作業を実施。
07出荷
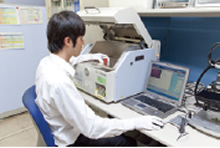
仕上がった製品を出荷前に綿密に検査します。また、新規材料に対して環境チェックを行っており、蛍光X線分析装置でめっき浴の種類別に環境監視も実施。
主要生産設備
- 射出成形機
- 8台
- トルクパックプレス機
- 2台
- リンクプレス機
- 8台
- 高速自動プレス機
- 1台
- マシニングセンター
- 2台
- ワイヤー放電加工機
- 2台
- NCフライス盤
- 1台
- NC放電加工機
- 1台
- 成形平面研削盤
- 3台
- 旋盤
- 1台
- 三次元成型部品試作機
- 1台
- その他電気系計測器
- 一式